RookieTJx2
Knows what a fatty is.
- Joined
- Apr 28, 2014
- Location
- Indiana
Haven't gotten as much done as I've wanted, but pesky things like work keep getting in the way.
Anyway...
I welded the backside of the side of the smoker.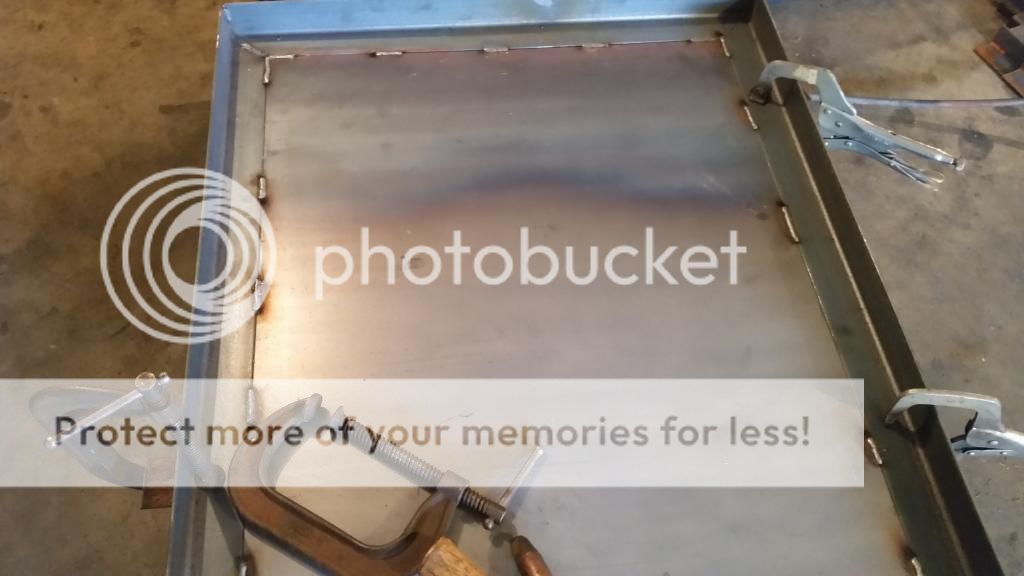
Then I drilled a hole in the side to run a piece of pipe. This will be to run a probe thermometer through the side without having to smash it in the door. When not being used, it can be plugged. Then I welded the pipe in place.


Next, I welded and cleaned up the inside so it will be ready for the next step.
Welded in the front...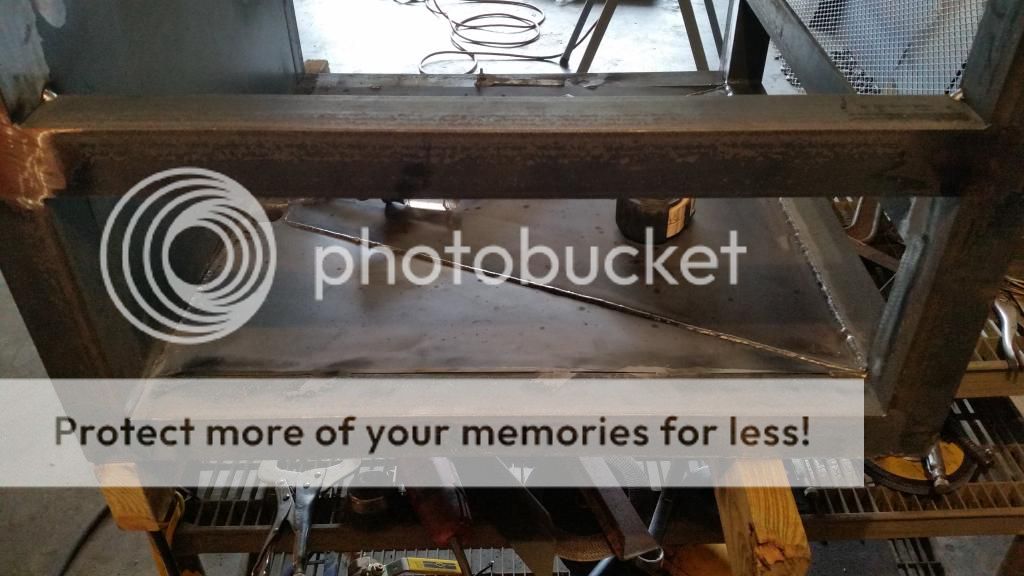
And added a brace for tuning plates. Will it need tuning plates? I don't know, but it's a lot easier to do it now then to add it later.

I also added the fire box to cook chamber opening.
BTW, I added a new tool to my garage.
Where has this been all my life? It cuts through metal with ease and leaves a nice, burr free edge.
That's it for now...
Anyway...
I welded the backside of the side of the smoker.
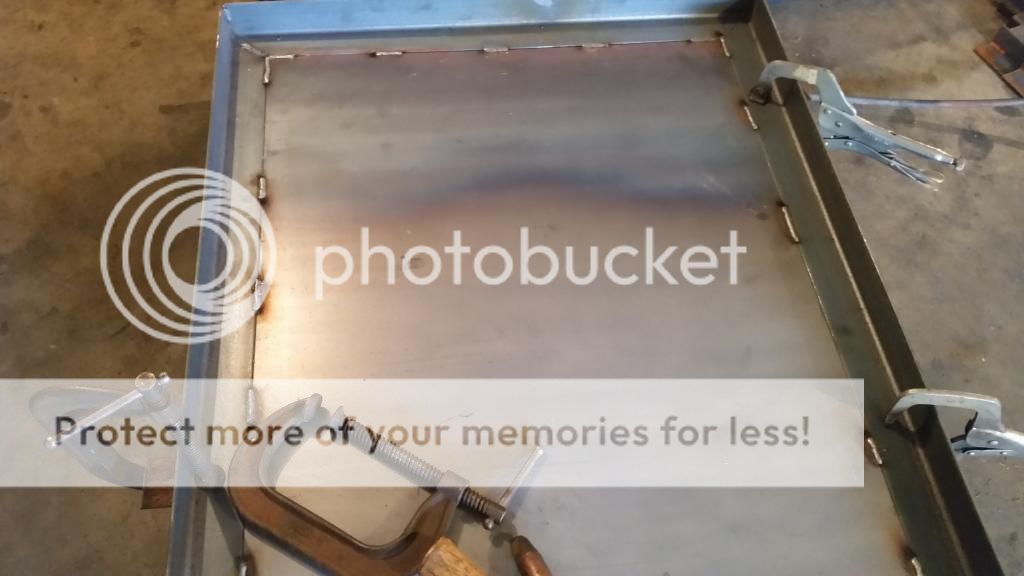
Then I drilled a hole in the side to run a piece of pipe. This will be to run a probe thermometer through the side without having to smash it in the door. When not being used, it can be plugged. Then I welded the pipe in place.


Next, I welded and cleaned up the inside so it will be ready for the next step.

Welded in the front...
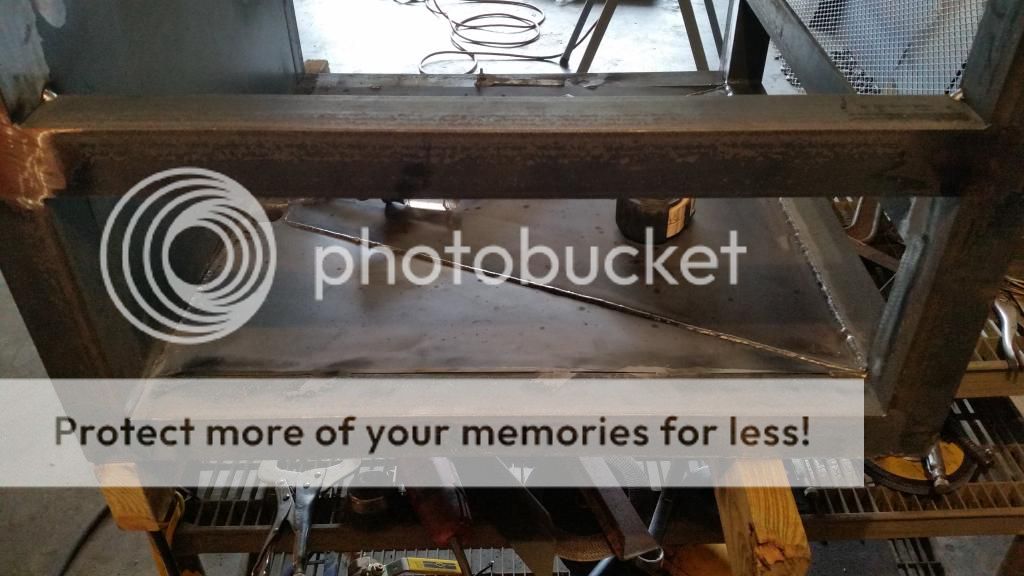
And added a brace for tuning plates. Will it need tuning plates? I don't know, but it's a lot easier to do it now then to add it later.

I also added the fire box to cook chamber opening.

BTW, I added a new tool to my garage.

Where has this been all my life? It cuts through metal with ease and leaves a nice, burr free edge.
That's it for now...